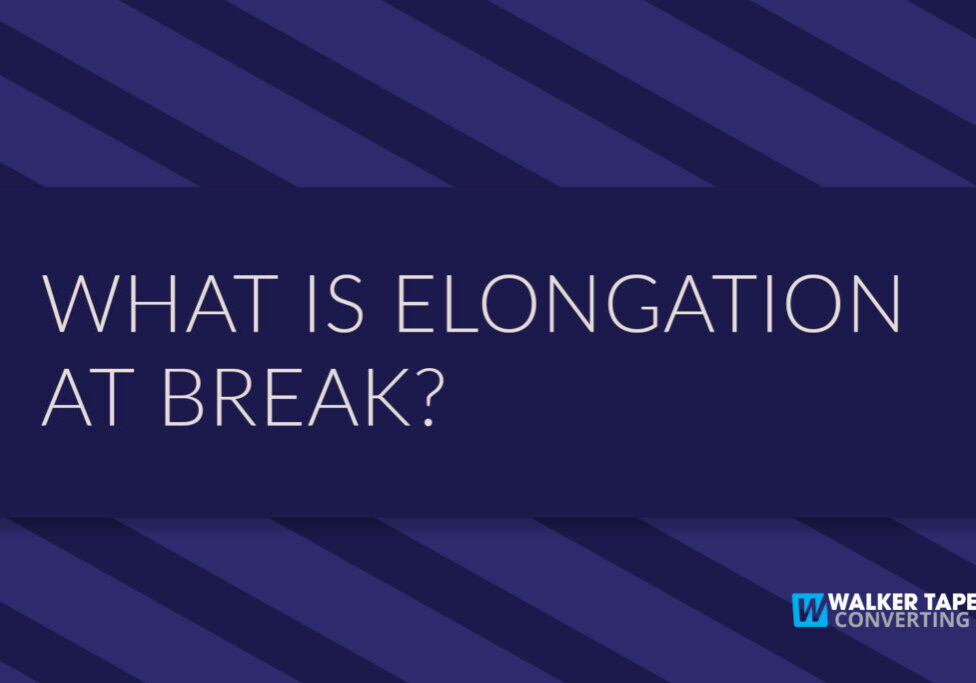
There are a lot of performance traits made available on a tape’s technical data sheet: temperature resistance, UV resistance, chemical resistance, adhesion strength, etc. But one of the weirder phrases you often come across has to be elongation at break.
In Terms of Tape, What Is Elongation at Break?
Elongation at break is simply how long a tape can stretch before breaking when pulled from both ends.
On data sheets, you find a tape’s elongation at break as a percentage. This percentage represents how much of a tape’s original length can be pulled before breaking. For example, a 12-inch piece of tape with a 50% elongation at break can stretch an additional six inches before it reaches its breaking point. Sometimes, you can also find it called fracture strain, but not by us in the rest of this blog post.
What is the Difference Between Tape’s Tensile Strength & Elongation at Break?
Tensile strength measures the force needed to break tape apart. It’s measured by the pounds of force applied per square inch of tape. This definition sounds quite similar to elongation at break, however, there is an important distinguishing factor.
Both concepts deal with tensile force or pulling at the ends. But tensile strength and elongation at break measure two different qualities of the tape.
Since tensile strength measures the force needed to break tape apart, it deals with external traits acting on the tape. Elongation at break, on the other hand, focuses on the internal traits that allow a tape to function and hold itself together.
So, knowing a tape’s tensile strength comes in handy for applications where you know involve a certain amount of stress pulling on the tape. This shows you if the tape solution works with the machinery or production/application process that you use.
Knowing a tape’s elongation at break gives you an idea if the tape itself has the stretchable nature to perform how you need it to.
Why Does Elongation at Break Matter to Tape?
Depending on the application, elongation at break can matter a great deal. Think of all the ways we apply tape that involves some amount of our pulling on the tape. These include obvious examples such as fixing surface protection tape and then pulling it tightly to ensure a straight, clean line (like with masking tapes).
Then there are also challenging applications that involve taping tight corners or curves. When you need a highly conformable solution for irregular shapes, it makes the process much more streamlined if the tape you’re working with has good elongation at break.
But there are also less obvious examples, such as taping layers of foam together to create a mattress. If done with too much slack, there can be wrinkles and air bubbles in the tape that affect the finished product.
This performance trait applies to much more than mattress production. In fact, in most processes where you are laminating layers of flexible materials together, this ability to stave off wrinkles and air bubbles comes in handy.
Elongation at break also matters to tapes in temperature variable conditions. The tapes and the materials they’re bonded to expand and contract based on temperature changes. The ability of a tape to conform with and support these changes in form increases its overall bond performance.
One tape construction that is famous for its ability to compensate for materials expanding and contracting in temperature changes is high bond tapes. These options are usually made by infusing their foam carrier with adhesive. This reinforces the tape’s foam carrier, essentially making it the adhesive itself.
The elongation at break for high bond, foam core tapes are often off the charts at 1000%. Again, this means that the tape could be stretched to a thousand times its length before failing.
Elongation at break also serves another function in terms of a tape’s performance relative to temperature. As it gets colder, tape adhesives become harder.
This hardening gives the tape a more glassy nature, prone to becoming brittle and cracking. But the more elongation at break a tape is capable of, the more flexible the tape is likely to stay as temperatures go down. They too harden, as all tapes do. But they won’t harden as much or as quickly compared to options with lower elongation at break percentages.
Are you working with tape in an application where flexibility, conformability, and stretchability are important? Send us a free quote request, and we can find you the right tape with the perfect elongation at break for your project!