What Is a Membrane Switch?
What’s a Membrane Switch?
A membrane switch is a human-machine interface (HMI) made of flexible materials and printed conductive inks. That’s the wonky answer. Basically, if you’re working with remotes, keypads, keyboards, or display controls outside of touch screens or actual mechanical buttons and knobs and such, then you’re most likely using a membrane switch.
In fact, the name turns out to be quite literal. As illustrated below in much more detail, a membrane switch entirely consists of thin, flexible layers (aka membranes).
Two general types exist: tactile and non-tactile. Tactile membrane switches incorporate domes to give the feeling of pressing a button. Non-tactile membrane switches go without the domes, yet they often include audio or LED indicators to illustrate when a button’s pressed.
While tactile options tend to offer a more satisfying user experience (entire cartoons exist about the thrill of pushing a button), non-tactile choices tend to be more affordable. In some cases, they even last three times as long as their tactile counterparts.
Regardless of which type you choose, they have surprising advantages over other HMIs (touch screens and mechanical switches) and require custom converted tape to achieve those advantages.
Applications
- Consumer electronics
- Remotes
- Heating/cooling controls
- Security Keypads
- Computer keyboards
- Household appliances (washing machines, microwaves, coffee makers, exercise equipment, etc)
- Medical/Dental equipment
- Emergency call buttons
- Patient monitoring systems
- Surgical equipment
- Staff communications devices
- Drug delivery systems
- Hospital beds
- IV pumps
- Analytical equipment
- Feeding pumps
- Industrial machinery
- Laboratory equipment
- Agricultural machinery
- Military technology
- Aerospace/marine control boards
- Gas pumps
- Food service controls
How Do Membrane Switches Work?
First developed in the late 1970s, innovations in membrane switch technologies have come a long way. In general, how a membrane switch works involves a continuous open circuit running through the bottom circuitry’s conductive inks. When pressed by an operator, the top circuit contacts and momentarily shorts the bottom open circuit. The short signals the desired action to the machine.
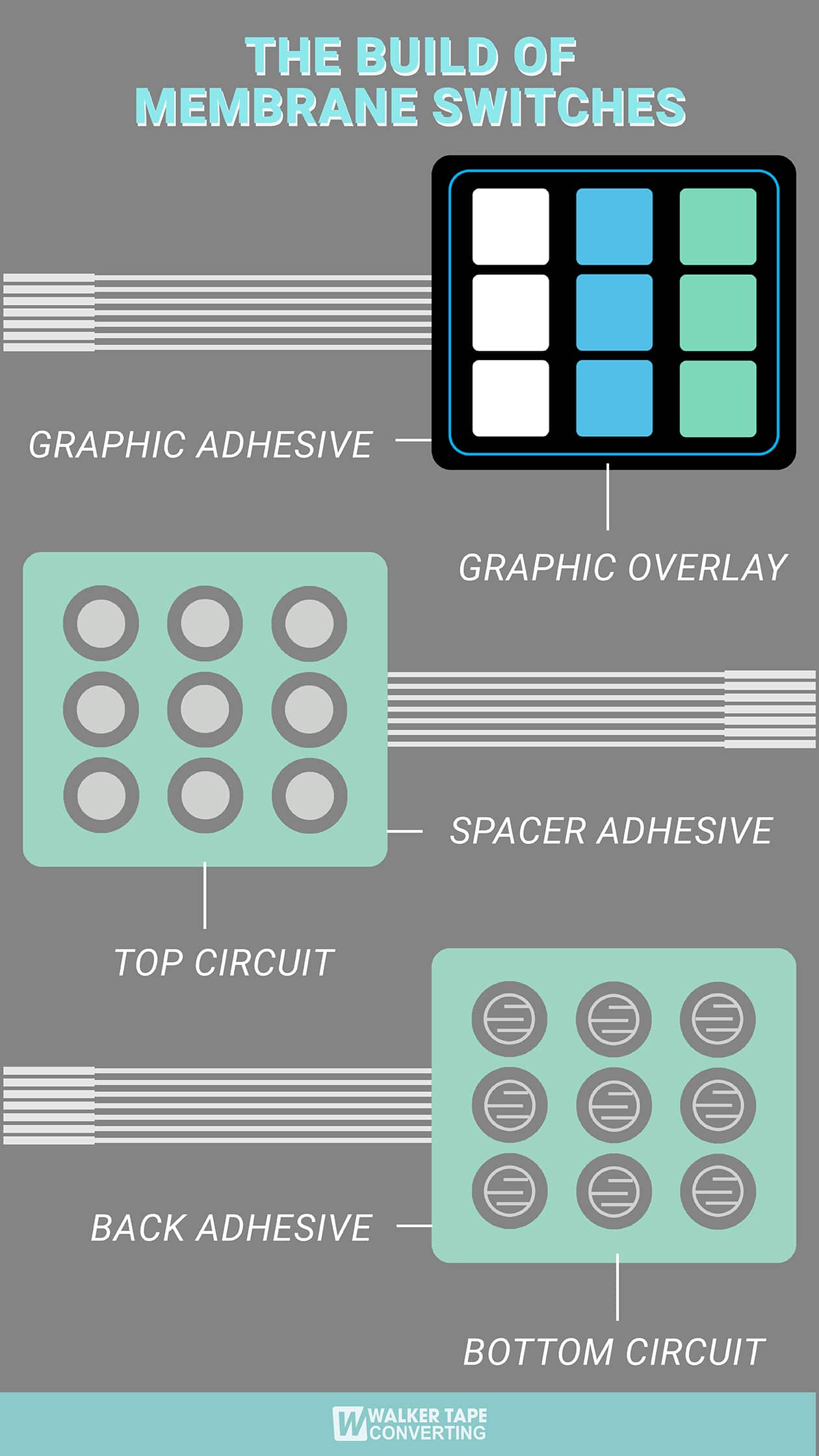
- Graphic overlay: The interface layer consisting of the buttons and display that the operator sees and interacts with.
- Graphic attachment adhesive: The adhesive layer that attaches the graphic overlay to the top circuit layer. The adhesive must be uniquely die cut to match the graphic overlay design as well as the outside dimensions of the membrane switch.
- Example Tape Choice: 3M™ Graphic Attachment Adhesive 9045MP
- Top circuit: The circuitry closest to the interface layer that, when pressed, hits the desired area on the bottom circuit layer.
- Spacer adhesive: The adhesive that separates the circuit layers from each other. This membrane switch spacer, just as with the graphic attachment adhesive, requires a unique die-cut exactly matching the interface design of the graphic overlay and outside dimensions of the switch.
- Example Tape Choice: 3M™ Membrane Switch Spacer 7956MP
- Bottom circuit: The circuit running a continuous current through conductive inks (often silver, copper, or graphite.
- Backer adhesive: Used to mount the membrane switch to the desired application. This final mounting adhesive also must fit the unique die-cut shape of the switche’s outside dimensions.
- Example Tape Choice: 3M™ Switch Attachment Adhesive 467MP
The Vital Role of Die-Cut Tapes
As you can see from both the infographic and the rundown of a membrane switch’s construction, three layers of the device depend on die-cut adhesive technology. Half of the membranes needed to make the switch need adhesive layers that match the outside dimensions as well as the uniquely designed interface buttons.
Each membrane switch application has different constraints. They need to meet certain sizes, shapes, and room for other aspects of the product’s ultimate design. With each required specification comes the need for die-cut layers of adhesive to match.
A membrane switch’s graphic overlay is endlessly customizable from logos and fades to complex multi-color designs and sleek presentations. As a custom tape converter, we can both find you the adhesives that work best for the materials of your switch and, most importantly, die-cut your adhesive layers precisely to achieve your project’s exact design.
Should You Go with Touch Screen, Membrane, or Mechanical Switches?
(Disclaimer: Considering how membrane switches require our tape converting services, it may seem biased for us to participate in this discussion. However, we also convert tapes for touch screens, knobs, dials, and various buttons on mechanical switches. Our passion’s in providing the tape needs you have, regardless of which HMI you choose.)
It depends. Industries across the board require HMIs, and every application comes with different requirements. Touch screens go a long way to save energy. Certain regulations and codes may require mechanical options. It just really depends.
Several articles out there create a versus mentality when it comes to these options (membrane vs mechanical switches). But, to maximize access to all the advantages of these technologies, we should reframe the discussion more around how they complement each other. Even in our examples below, notice how several of the photographs show applications that use a combination of HMIs.
Instead of trying to convince you to only depend on membrane switches, the following considers their advantages more to illustrate ways they could complement your HMI product. With so much focus going to touch screens, it’s good to be reminded of other innovative choices available.
More Durable
Due to the die-cut tapes holding everything together, membrane switches are completely sealed from moisture and hazardous chemicals. So, for industries exposed to the elements or strong chemicals, they’re ideal. This resistance is a main reason why membrane switches contribute to fueling stations, production floors, medical facilities, laboratories, exercise gyms, and kitchens. They’re much more reliable around moisture and chemicals than touch screens and mechanical switches.
Beside protection against environmental factors, their flexible construction supported by thin, conformable tapes also protects them from aggressive use and impact accidents. Mechanical switches include several moving parts that break or snap off, whereas a membrane switch’s interface is simply one continuous layer. Touch screens are mostly sealed with glass, which immediately makes them susceptible to breakage. Americans alone spend nearly three-and-a-half billion dollars a year replacing their phones due to shattered screens. That’s two touch screens breaking every second (and that’s just in the smartphone industry).
Easier to Clean
Another main reason we see membrane switches all over the place in medical facilities and gyms has to do with how hygienic they are. Crevices between buttons on mechanical switches traps contaminants and germs.
But since membrane switches are free from any crevices and the die-cut tape layers seal them completely, we can clean them, wipe them down, and sterilize them quickly and easily.
More Accessible
Touch screens, for various reasons, come with more user error. In 2017, complications with touch screen technologies played a tragic role in an accident where a US Navy destroyer collided with a tanker, killing 17 sailors. When surveyed, sailors “overwhelmingly” preferred using tactile controls that offered more peace of mind, such as buttons, wheels, and throttles. Mechanical and domed membrane switches offer the peace of mind with better precision and a more satisfying tactile user experience.
What if you must use HMIs wearing gloves? That simple barrier rules out touch screens altogether, as do other considerations. Membrane switches work much better for various people with disabilities (auditory, visual, physiological, developmental, etc). Plus, how dangerous would hospital bed equipment be if it always required a perfectly steady hand to make emergency alerts?
Easier to Design
When it comes to space, mechanical switches and touch screens take up a lot of it. The technology needed for touch screens requires a thick housing, especially in comparison with membrane switches. A membrane switch’s thin, low profile saves an incredible amount of space and makes a designer’s job way easier to integrate the HMI into the product.
More Affordable
Of any of these three HMI options, membrane switches offer the best price point. Again, since they are so much easier to produce (one integrated switch instead of several individual moving parts), they prove the lowest per-piece price and also the lowest tooling costs.
This could be refreshing to hear if you’re in the consumer electronics industry where the profit margins can be quite a bit slimmer.
Easier to Customize
Even though they surround us in various forms, membrane switches sometimes get thought of as looking too old school or industrial. But if you can print a design, then you can give your membrane switch that look.
In truth, so many designers are making such creative custom membrane switch graphics that we often confuse them for touch screens.
Have the perfect membrane switch design in mind? Save time and money, and ask us for a free custom quote today.