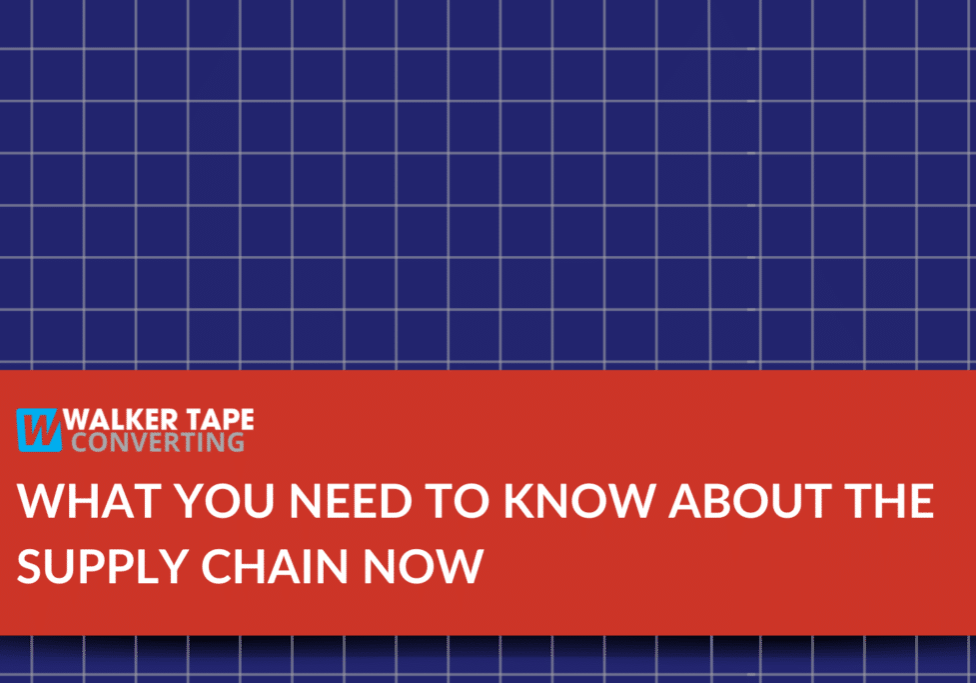
Supply chain disruption has, unfortunately, become a phrase people are all-too-familiar with. It has hit every industry, every sector and every household since the pandemic began. It brought the global economy to a full stop as businesses in all sectors, all industries and all countries closed up shop. What’s the current state of the supply chain and, given the looming recession, can we expect more of it?
Here’s an update on where things stand now.
First, the bad news.
According to the National Association of Manufacturers (NAM), supply chain disruption will likely continue throughout 2023. This, from a recent survey, Resilient M4.0, conducted by NAM’s Manufacturing Leadership Council.
Some highlights from the survey:
- 90% have experienced significant or partial disruption since the pandemic’s onset
- 73% say their supply chains are not fully protected
- 19% believe their supply chains are integrated
Ongoing disruption factors include continuing lockdowns in China, clogged shipping lanes, shortages of trucks and drivers to take containers to their destinations when they do finally arrive, and general employment problems all along the supply line. These factors are nothing new — manufacturers have been dealing with them, and attempting to find creative workarounds, since the pandemic hit U.S. shores two years ago.
But new variables are coming into the mix as well. Let’s look at a few of those.
Extreme weather. Those 100-year floods, worst-ever hurricanes and ongoing wildfires seem to be becoming the norm, knocking out power and delaying shipments worldwide.
Inflation. New research by Accenture finds a strong correlation between supply chain disruption and inflation. Increased costs all along the supply chain drive inflation, which raises prices, which lead to greater inflation. It’s a cycle.
China’s ongoing “zero tolerance” COVID policy. In China, when COVID infections crop up in any given city, that city is put on immediate lockdown. If your company or your vendors are importing goods, parts, materials or otherwise from China, those shipping disruptions are still a way of life, and will continue to be for the foreseeable future.
The war in Ukraine. One of the major factors coming out of the war for manufacturers is the rising cost of fuel to transport products, parts and materials to manufacturing facilities. Tape giant 3M expects continued supply chain holdups because of it.
Now, the good news.
At Walker Tape Converting, we’ve been extremely fortunate to have experienced very little disruption, and as such, our customers have experienced very little disruption and delay as well. How have we been able to successfully navigate this worldwide supply chain shortage and get our customers the products they need? Two reasons. Relationships we’ve built over the years, and a variety of choices.
Relationships. We’ve been in this business for more than 30 years, and during that time, we’ve developed strong relationships with our suppliers. We know who to turn to when we hit a snag, who might have product or materials that we don’t have, and who can help out when we need a favor. In short, we’ve got connections all up and down the supply chain to ensure we can deliver for our customers.
Choice. Unlike most other converters, we’re not tied to just one tape manufacturer. It’s no secret 3M has been experiencing continued supply chain disruption — it’s all over the news. Fortunately, we have other manufacturers to turn to, including European tape powerhouse tesa, and Avery Dennison, known for their highly innovative tape creations. By having close relationships with many different manufacturers, and preferred status with the three biggest tape manufacturers in the world, we are able to circumvent supply chain disruptions and deliver for our clients.
We’re proud to say we’ve been able to meet our customers’ needs, even throughout the pandemic and beyond. Whatever may come, Walker Tape has your back.